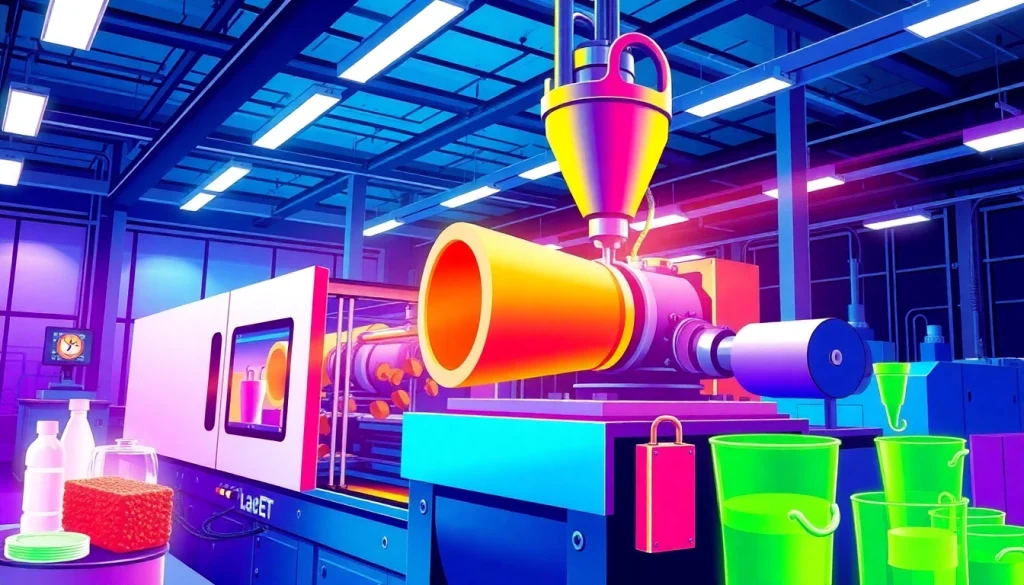
Understanding Blow Moulded Plastic Parts
Blow moulded plastic parts are a cornerstone of modern manufacturing, offering versatility and efficiency in producing complex hollow shapes. This manufacturing process involves inflating a heated plastic tube (known as a parison) in a mould cavity, allowing it to take the shape of the mould while creating a hollow interior. The applications of blow moulded plastic parts extend across various industries, such as packaging, automotive, and consumer goods. Understanding the intricacies of this process can provide valuable insights into optimizing part design and selecting the right manufacturing methods.
1. What are Blow Moulded Parts?
Blow moulded parts are produced through a process that uses air pressure to form plastic into specific shapes. This technique is primarily used to create hollow items such as bottles, containers, and various components used in automobiles and appliances. The blow moulding process can be classified into three main types:
- Extrusion Blow Moulding (EBM): A continuous process where plastic is melted and extruded into a hollow tube, which is then inflated into the mould.
- Injection Blow Moulding (IBM): A two-step process that involves injecting plastic into a preform shape before it is blown into the final product’s shape.
- Injection Stretch Blow Moulding (ISBM): This method combines the injection and stretching processes to improve the strength and clarity of the final product, often used for PET bottles.
2. Common Applications of Blow Moulded Plastic Parts
Blow moulding technology is utilized in various sectors, showing its adaptability and efficiency:
- Consumer Packaging: This includes plastic bottles for beverages, detergents, and personal care products.
- Automotive Industry: Parts such as fuel tanks, air ducts, and various hollow components are manufactured using blow moulding.
- Industrial Applications: Components for machines, equipment housing, and storage containers.
- Healthcare: Medical devices and products that require sterile, lightweight hollow shapes.
3. Key Benefits of Blow Moulding Technology
The blow moulding process has several advantages that make it a preferred choice in manufacturing:
- Cost-Effectiveness: The ability to produce large batches efficiently lowers production costs.
- Design Versatility: Complex shapes can be created with varying wall thicknesses.
- Material Efficiency: Minimal material waste is generated during production, and the process accommodates various plastic types.
- Lightweight Products: Blow moulded parts are often lighter than their traditional counterparts, contributing to overall efficiency.
The Blow Moulding Process Explained
1. Overview of the Blow Moulding Techniques
The blow moulding process can be broken down into several steps, providing a clearer understanding of how high-quality plastic parts are formed:
- Heating: The plastic material is heated until it reaches a molten state.
- Forming the Parison: A plastic tube (parison) is formed through either extrusion or injection.
- Blowing: The parison is placed into the mould, where compressed air is injected, causing the plastic to expand and take the shape of the mould.
- Cooling: The mould is cooled to solidify the shape of the plastic.
- Ejection: The solidified part is removed from the mould for quality inspection.
2. Materials Used in Blow Moulding
A variety of materials can be utilized in the blow moulding process, with each providing unique characteristics:
- Polyethylene (PE): Available in high-density (HDPE) and low-density (LDPE) forms, known for flexibility and chemical resistance.
- Polypropylene (PP): Strong and rigid, making it ideal for items requiring durability.
- Polyethylene Terephthalate (PET): Commonly used for bottles, recognized for its clarity and recyclability.
- Polyvinyl Chloride (PVC): Often used in applications requiring excellent weather resistance.
3. Quality Control in Blow Moulding
Ensuring quality in blow moulding involves various techniques and inspections at different stages of the production process:
- Material Inspection: Raw materials are evaluated for composition and consistency before processing.
- Mould Maintenance: Regular maintenance of moulds ensures consistent product quality and reduces defects.
- Process Monitoring: Real-time monitoring of temperature and pressure during production helps maintain optimal conditions.
- Final Product Testing: Finished parts undergo testing for mechanical properties, dimensions, and compliance with safety standards.
Design Considerations for Blow Moulded Plastic Parts
1. Factors Influencing Design Choices
Several factors impact the design decisions when creating blow moulded parts:
- Part Function: The intended use of the part dictates its shape, size, and material choice.
- Manufacturing Costs: Complexity of design can increase manufacturing time and costs, so efficiency is key.
- Durability Requirements: The end product’s exposure to stress or harsh environments influences material and design selection.
- Aesthetic Factors: Surface finish and appearance can impact consumer acceptance, especially in retail products.
2. Optimizing Part Design for Manufacturing
Optimization in design ensures that the manufactured parts meet specifications while maintaining efficiency:
- Simplifying Geometry: Designing parts with fewer features can minimize costs and improve cycle times.
- Standardizing Dimensions: Utilizing industry-standard sizes can reduce tooling costs and increase production rates.
- Incorporating Ribs and Supports: Strategic placements of ribs can enhance part strength without significantly adding weight.
- Draft Angles: Integrating draft angles in designs facilitates easier part ejection from the mould.
3. Innovations in Blow Moulded Part Design
The continuous evolution of manufacturing technologies also drives innovation in blow moulded part design:
- 3D Printing Integration: Combining 3D printing and blow moulding allows for rapid prototyping and more complex designs.
- Smart Technologies: Integrating sensors and RFID tags into products can enhance functionality and traceability.
- Eco-Friendly Materials: Utilizing biodegradable materials is gaining traction in response to sustainability concerns.
- Design Software: Advanced software solutions help designers simulate and optimize blow moulded parts using virtual modelling.
Choosing the Right Manufacturer for Blow Moulded Parts
1. Evaluating Manufacturer Capabilities
Selecting a reliable manufacturer is critical to ensure that blow moulded parts meet quality expectations:
- Experience: Look for manufacturers with a proven track record in producing similar parts.
- Technology: Confirm that they employ modern blow moulding techniques and equipment.
- Compliance: Assess whether they adhere to relevant industry standards and regulations.
- Certifications: Seek manufacturers with certifications such as ISO 9001, which indicates quality management practices.
2. Comparing Costs and Quality
A cost-quality balance is essential when selecting a manufacturer:
- Get Multiple Quotes: Obtain detailed quotes from several manufacturers to compare costs while factoring in quality.
- Assess Production Times: Ensure that lead times align with your project’s deadlines to avoid disruptions.
- Evaluate Total Cost of Ownership: Consider long-term costs, including maintenance, warranties, and delivery to gauge overall value.
- Conduct Trials: Request sample runs to evaluate the quality of the parts before committing to larger orders.
3. Understanding Lead Times and Minimum Orders
Lead time and order minimums can significantly affect project schedules:
- Establish Timeline Requirements: Clearly communicate deadlines to ensure the manufacturer can meet your needs.
- Clarify Minimum Order Quantities: Understanding the minimum quantity of parts that can be produced helps in planning your procurement strategy.
- Factor in Tooling Time: Custom tooling can increase lead times, so consider this when planning production runs.
- Flexibility: Choose a manufacturer that shows flexibility in order sizes and modification requests to adapt to changing needs.
Future Trends in Blow Moulding Technology
1. Advancements in Blow Moulding Equipment
The blow moulding industry is witnessing significant advancements in technology:
- Automation: Increased automation enhances efficiency, reduces labor costs, and improves precision.
- Smart Manufacturing: Implementation of IoT devices enables real-time monitoring and predictive maintenance of machinery.
- Energy Efficiency: New energy-efficient machines are being developed to reduce the environmental impact of manufacturing processes.
- Advanced Cooling Systems: Innovations in cooling techniques allow for faster cycle times, improving productivity.
2. Sustainable Practices in Blow Moulding
With growing environmental concerns, the focus is on sustainable manufacturing methods:
- Recycling Materials: Incorporation of recycled plastics in the production process supports the circular economy.
- Reducing Waste: Implementing lean manufacturing techniques can minimize scrap and optimize material usage.
- Eco-Friendly Designs: Developments in design encourage smaller, lighter products that use less material without sacrificing functionality.
- Lifecycle Assessment: Comprehensive assessments are increasingly used to evaluate the environmental impact of products from creation to disposal.
3. The Future of Blow Moulded Products in Various Industries
The versatility of blow moulded products suggests a bright future across different sectors:
- Consumer Goods: Continued innovation will likely yield environmentally friendly products that appeal to eco-conscious consumers.
- Medical Applications: The demand for high-quality medical devices driven by health awareness will lead to advancements in blow moulding technologies.
- Automotive Innovations: As vehicle designs evolve towards lightweight materials that enhance fuel efficiency, blow moulded parts will find increased utilization.
- Aerospace Development: Emerging uses in aerospace for lightweight components will necessitate advanced blow moulding techniques to meet stringent standards.