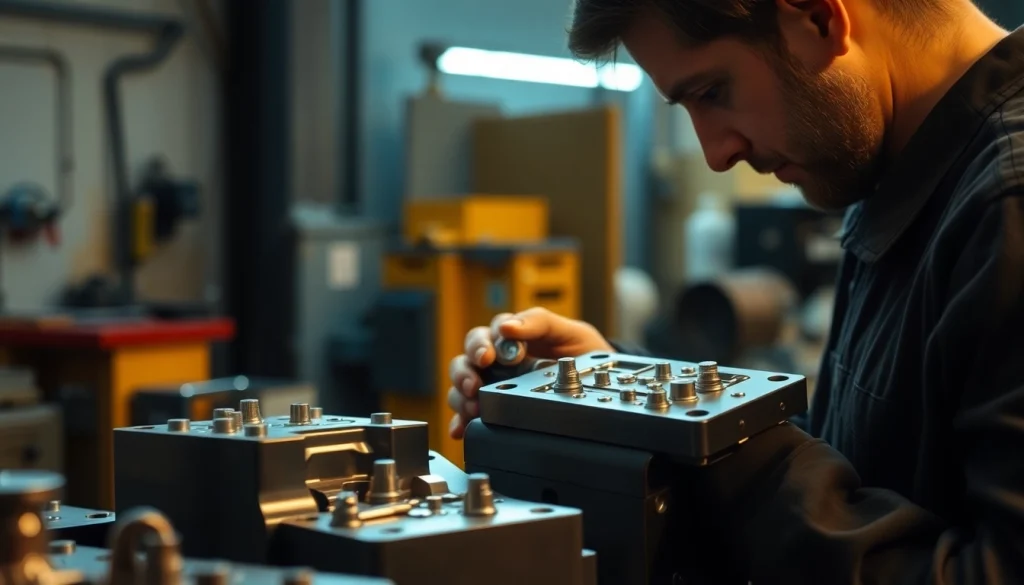
Understanding the Role of a Mold Maker for Injection Molding
The process of creating high-quality molded plastic parts relies heavily on the expertise of a mold maker for injection molding. This skilled profession involves a combination of artistry and engineering aimed at producing molds that can withstand the rigors of industrial production. A competent mold maker understands not only the intricacies of mold design but also the importance of precision and sustainability in the manufacturing process.
Definition and Key Skills
A mold maker is a specialized artisan who fabricates molds that are essential in the casting and injection molding processes. To excel in this role, individuals must demonstrate a unique blend of skills:
- Technical Proficiency: Mastery of machining and CAD software is critical.
- Detail Orientation: Precision in measurements and fabrication is paramount.
- Problem-Solving: The ability to troubleshoot design and manufacturing issues is essential.
- Material Knowledge: Understanding various molding materials, their properties, and suitability for different applications.
Importance in the Manufacturing Process
Mold makers are pivotal in the injection molding industry as they create molds that define the shape and finish of the final product. Their expertise directly impacts the efficiency of the production process, the quality of the end products, and ultimately, the bottom line for manufacturing businesses. A skilled mold maker ensures that molds are constructed to exact specifications, which minimizes waste and enhances consistency in mass production.
Common Materials Used in Mold Making
When creating molds for injection molding, various materials can be employed, depending on factors such as the type of plastic used and the intended production volume. The most common materials include:
- Steel: Often chosen for durability and longevity, particularly in high-volume applications.
- Aluminum: Preferred for lower-volume applications due to its cost-effectiveness and ease of machining.
- Silicone: Used in specific cases, primarily for prototypes or small batch runs.
- 3D Printed Materials: Increasingly utilized for rapid prototyping and complex designs.
How to Select a Reliable Mold Maker for Injection Molding
Selecting the right mold maker can significantly influence not just the quality of the molds produced but also the overall success of your manufacturing operations. To ensure you partner with a competent mold maker, here are some crucial steps to consider.
Evaluating Qualifications and Experience
The qualifications of a mold maker can offer insight into their capacity for delivering quality work. Key factors to evaluate include:
- Education: A background in machining or engineering can be advantageous.
- Experience: Look for mold makers with a proven track record in your specific industry.
- Certifications: Certifications from recognized institutions can indicate professionalism and expertise.
Factors to Consider When Choosing a Partner
Several critical factors should influence your decision as you contemplate a mold maker. These include:
- Production Capacity: Ensure the mold maker can meet your production volume needs.
- Technology: Evaluate their manufacturing technology to ensure they utilize up-to-date methodologies.
- Location: Proximity can affect communication, lead times, and shipping costs.
- Reputation: Research reviews, testimonials, and case studies to understand their reliability.
Questions to Ask Potential Mold Makers
When interviewing potential mold makers, consider asking the following questions to gauge their capabilities:
- What types of molds do you specialize in?
- Can you provide examples of similar projects you have completed?
- What is your typical turnaround time for mold fabrication?
- How do you handle quality control and testing?
- What materials do you recommend for my specific application?
The Process of Injection Mold Making
Understanding the injection mold making process can provide valuable insights into how different stages contribute to the overall quality of the final product. Here’s an overview of the key steps involved:
Step-by-Step Overview of Mold Production
The process of injection mold making can be broken down into several distinct phases:
- Design: The first step involves creating a detailed design and blueprint using CAD software.
- Material Selection: Choosing suitable materials based on production requirements and cost considerations.
- Machining: Utilizing CNC machines and other equipment to carve the mold from the selected materials.
- Assembly: Once machined, the mold components are assembled.
- Testing: Rigorous testing is conducted to ensure the mold performs as intended.
- Finishing: Finally, the mold undergoes finishing processes to improve surface quality and durability.
Advanced Techniques and Technologies
As technology evolves, so do the methods used in mold making. Some advanced techniques include:
- 3D Printing: Utilized for rapid prototyping and creating complex geometries.
- Electrical Discharge Machining (EDM): Allows for the creation of intricate designs not achievable through traditional machining.
- Finite Element Analysis (FEA): Used to simulate the behavior of molds under stress, thus enhancing design accuracy.
Quality Assurance in Mold Manufacturing
Quality assurance is a fundamental aspect of mold making and involves rigorous testing and inspections of molds before they are approved for production. Typical quality checks include:
- Dimensional Accuracy: Ensuring that every part of the mold matches the design specifications.
- Material Integrity: Testing the materials used for durability and performance under operational stresses.
- Surface Finish: Evaluating the surface finish for smoothness to minimize defects in molded products.
Cost Considerations for Hiring a Mold Maker for Injection Molding
Understanding the costs associated with hiring a mold maker is essential for budgeting and financial planning in any manufacturing operation. Various factors can influence mold making costs, including:
Average Pricing and Factors Affecting Costs
The price of creating injection molds can vary widely depending on several factors:
- Complexity: More intricate designs require advanced tooling and therefore cost more.
- Material Choices: The type of material selected for mold production can drastically affect pricing.
- Production Volume: Higher volumes usually lead to cost savings per unit.
For instance, basic molds could range from $3,000 to $10,000, while complex multi-cavity molds might exceed $50,000.
Budgeting for Different Mold Types
When budgeting for mold production, consider the following:
- Initial Investment vs. Production Cost: Understand that while the upfront costs can be significant, quality molds can save money in the long run by reducing production downtime and scrap rates.
- Maintenance Costs: Molds require ongoing maintenance, which should be accounted for in your budget.
Long-term Financial Benefits of Quality Molds
Investing in high-quality molds can yield considerable long-term savings and benefits:
- Reduced Scrap Rates: Quality molds often reduce defects and scrap, improving overall efficiency.
- Extended Lifespan: Durable molds contribute to long-term production reliability.
- Improved Product Quality: Higher-quality molds lead to better product finishes, enhancing brand reputation.
Case Studies: Successful Projects by Top Mold Makers
The importance of selecting a proficient mold maker becomes evident through real-world examples. Exploring notable case studies can provide valuable insights into how expert mold makers have successfully navigated challenges to deliver exceptional molds and outcomes.
Industry Innovations and Their Impact
For instance, a leading mold maker developed a novel multi-cavity mold for a major electronics brand, allowing for the simultaneous production of intricate housings. This innovation reduced cycle times by 30%, resulting in substantial cost savings.
Challenges Overcome through Expert Mold Making
In another case, a mold maker faced challenges with a particularly complex part that required high precision. Through the implementation of advanced CAD simulations and iterative prototyping, they managed to achieve an accurate mold that met the client’s stringent specifications, leading to a successful product launch.
Lessons Learned from Real-World Applications
Successful projects highlight the importance of communication and collaboration between mold makers and manufacturers. By maintaining clear dialogue throughout the design and production phases, clients can ensure their requirements are understood, which ultimately leads to better outcomes and fewer iterations.