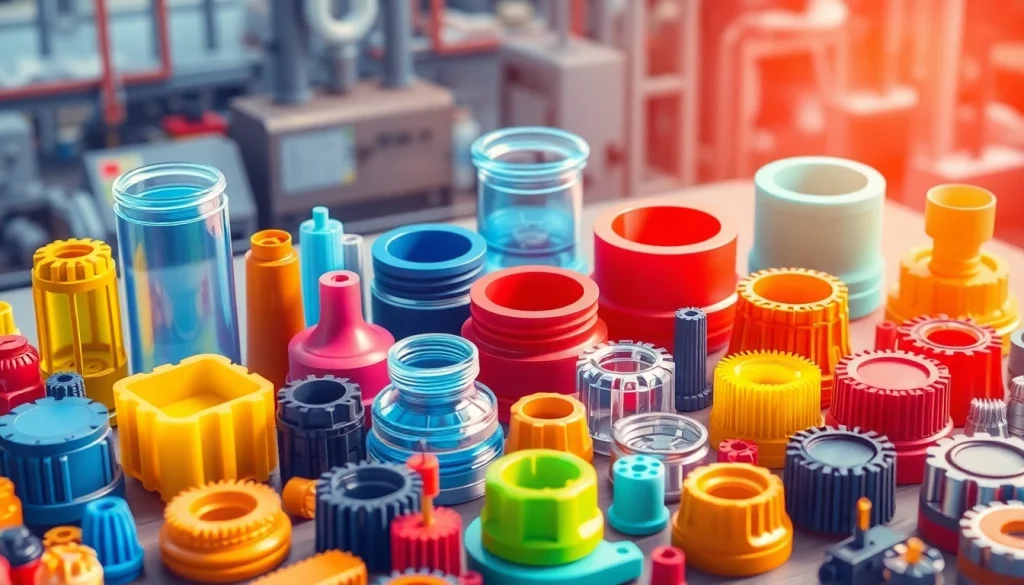
Understanding Injection Molded Parts
Injection molding plays a crucial role in the manufacturing industry, particularly in producing injection molded parts. These parts are created using a method that helps in achieving high precision, repeatability, and the ability to scale effectively, which makes it a favorable choice among manufacturers across various sectors. To understand injection molded parts, we first need to delve into their definition and key characteristics, the materials commonly used in the process, and the benefits they offer to manufacturers and consumers alike.
Definition and Key Characteristics
Injection molded parts are products produced through the injection molding process, where liquid material (usually plastic) is heated until it becomes fluid and then injected into a mold. This mold is specifically designed to the required specifications of the part, and once the material cools and solidifies, the mold is opened to release the final product. The key characteristics of injection molded parts include:
- Precision: Injection molding allows for tight tolerances and complex geometries to be achieved, making it ideal for components that require accuracy.
- Repetitiveness: Once the mold is created, the exact same part can be produced in high volumes with consistent quality and performance.
- Material Versatility: A wide variety of materials can be used in the process, including thermoplastics, thermosetting plastics, and elastomers, which can be tailored to specific applications.
- Cost-Effectiveness: Particularly for large production runs, injection molding can yield lower per-unit costs due to reduced waste and efficient processing times.
Common Materials Used in Injection Molding
Numerous materials can be employed in the manufacturing of injection molded parts, each offering unique properties suited for different applications. Here are some of the most commonly used materials:
- Thermoplastics: These are plastics that become pliable or moldable upon heating. Common examples include polyethylene (PE), polypropylene (PP), and polystyrene (PS). They are favored for their flexibility, lightweight nature, and excellent barrier properties.
- Thermosetting Plastics: Unlike thermoplastics, these materials harden upon heating and cannot be remolded. Examples include epoxy, phenolic, and polyurethane, which are used for their rigidity and thermal stability.
- Elastomers: These materials exhibit rubber-like elasticity and are ideal for seals, gaskets, and flexible components. Common elastomers used in injection molding include silicone and rubber.
Benefits of Using Injection Molded Parts
The benefits of injection molded parts extend beyond mere production capabilities. Manufacturers and designers benefit from several advantages:
- Efficiency: High-speed production capabilities mean that a large number of parts can be manufactured in a short timeline, leading to quicker time-to-market for new products.
- Reduced Waste: The injection molding process is optimized to minimize waste materials, as any excess can often be recycled back into production.
- Customization: Molds can be designed for specific needs, allowing for intricate designs and variations that meet customer specifications.
- Enhanced Product Performance: Injection molded parts can be engineered to offer high performance in terms of durability, resistance to heat, and other physical stresses.
Injection Molding Process: Step-by-Step
The injection molding process is intricate and involves several steps, each critical to producing high-quality parts. Understanding the machine components and how the process unfolds can provide insight into how to maximize efficiency and minimize errors.
Machine Components and Their Roles
To grasp the injection molding process, it’s essential to understand the key components of the injection molding machine:
- Hopper: This is where the plastic resin is fed into the machine.
- Heater: Surrounds the screw and barrel, providing the heat necessary for melting the plastic.
- Screw: A rotating device that moves the melted plastic toward the mold.
- Nozzle: The part that allows the molten plastic to flow into the mold.
- Mold: The custom-designed cavity that gives the part its shape.
- Ejector System: A mechanism that removes the finished part from the mold.
Step-by-Step Breakdown of the Process
Here’s a detailed breakdown of the injection molding process:
- Material Loading: Plastic pellets are loaded into the hopper.
- Melting: The heater melts the plastic as it is pushed forward by the screw through the barrel.
- Injection: The molten plastic is injected into the mold cavity under high pressure.
- Cooling: The material cools and solidifies, taking on the mold’s shape.
- Ejection: Once cooled, the mold opens, and the ejector system removes the finished part.
- Finishing: The part may undergo further finishing processes like trimming or painting, depending on the requirements.
Quality Control Measures
Ensuring quality in injection molded parts involves various measures, including:
- Regular Maintenance: Keeping machinery well-maintained prevents defects caused by wear and tear.
- Monitoring Machine Parameters: Key parameters such as temperature, pressure, and injection speed should be monitored closely throughout the process.
- Sampling and Testing: Regular inspection of parts helps identify any defects early in the production process, allowing for timely corrections.
Applications of Injection Molded Parts
Injection molded parts have an extensive range of applications across various industries due to their versatility and efficiency.
Industry-Specific Use Cases
The following list highlights specific industries that benefit from injection molded parts:
- Automotive Industry: Used for dashboards, interior panels, and exterior trim, enhancing both aesthetics and functionality.
- Consumer Electronics: Commonly used for casings, buttons, and other structural components, where precision and design are vital.
- Medical Devices: Injection molded parts are essential in creating surgical devices and packaging that maintain sterility.
- Packaging: Plastic containers such as bottles, caps, and trays are commonly manufactured using injection molding.
Everyday Products Made from Injection Molding
Many everyday items are made using injection molding, showcasing its widespread influence:
- Plastic bottles
- Cap lids
- Car parts
- Remote controls
- Toys, such as LEGO bricks
Innovative Designs and Custom Solutions
Due to its flexibility, injection molding can accommodate innovative designs. Manufacturers frequently collaborate with design engineers to create custom solutions, leading to new and unique products that might otherwise be impossible to produce.
Best Practices for Designing Injection Molded Parts
Effective design is crucial to successful injection molding, impacting factors such as production efficiency, part performance, and cost. Here are some essential considerations and strategies.
Essential Design Considerations
- Wall Thickness: Maintaining uniform wall thickness helps prevent warping and ensures even cooling.
- Draft Angles: Incorporating draft angles in the mold design facilitates easier ejection of parts.
- Corner Rounding: Sharp edges can lead to stress concentrations; rounding corners enhances durability and simplifies mold creation.
Avoiding Common Pitfalls
Many challenges can arise in the injection molding design process. Being aware of common pitfalls can help designers avoid them:
- Neglecting to consider shrinkage can lead to dimensional inaccuracies.
- Poor material selection may compromise the part’s strength and functionality.
- Overly complex shapes can increase costs and manufacturing difficulties.
Creating Efficient Molds
Efficient mold design is key to reducing production time and costs:
- Mold Variability: Use of interchangeable inserts can allow for adjustments without requiring new molds.
- Cooling System Design: Incorporating channels that optimize cooling can significantly reduce cycle times.
- Mitigation of Warpage: Design molds with features that reduce the likelihood of warpage during cooling.
The Future of Injection Molded Parts Manufacturing
The landscape of injection molded parts manufacturing is continuously evolving, driven by technological advancements and market demands.
Technological Advancements in the Industry
Some key technological trends shaping the future include:
- Automation: Increasing reliance on automation in the manufacturing process improves consistency and efficiency.
- 3D Printing: Emerging technologies are allowing for faster prototyping and more complex mold designs.
- Advanced Materials: Research into new materials is expanding the possibilities for more durable, lightweight, and sustainable products.
Eco-Friendly Practices and Materials
The industry is also moving toward sustainable practices, incorporating recyclable materials and energy-efficient processes to reduce environmental impact.
Market Trends and Predictions
With the continued growth of various consumer sectors, the demand for injection molded parts is expected to rise. Innovations and improvements in the technology and materials used will further enhance efficiency, reduce costs, and improve product quality.