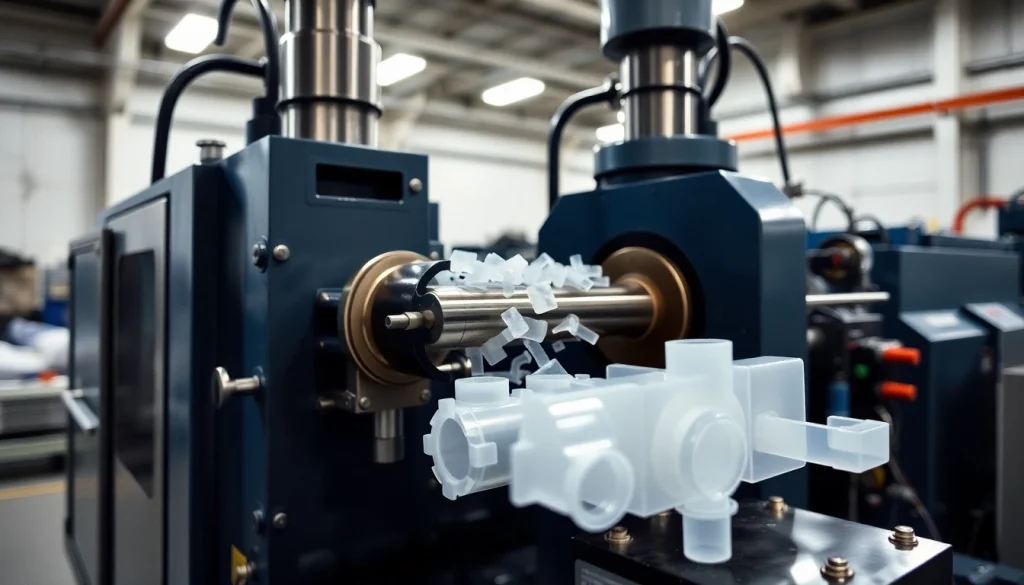
Understanding Blow Moulding Processes
What are Blow Moulded Plastic Parts?
Blow moulded plastic parts are hollow components produced through a specific manufacturing process known as blow moulding. This technique operates by inflating a heated plastic tube, or parison, which then takes the shape of a mould cavity, resulting in a wide variety of hollow parts, from bottles to intricate automotive components. This process is crucial for industries needing lightweight, robust, and durable parts.
Adopting methods such as blow moulded plastic parts allows manufacturers to create complex shapes that would be challenging or cost-prohibitive to achieve using traditional moulding techniques. Blow moulding excels in creating uniform wall thicknesses and enables high production yields, making it a staple in many sectors.
Types of Blow Moulding Techniques
Blow moulding techniques can broadly be categorized into three main types: extrusion blow moulding (EBM), injection blow moulding (IBM), and injection stretch blow moulding (ISBM). Each method has its specific applications, advantages, and limitations.
- Extrusion Blow Moulding (EBM): This method involves extruding a hot plastic tube which is then clamped in a mould and inflated. EBM is commonly used for creating large containers and hollow components due to its efficiency and cost-effectiveness.
- Injection Blow Moulding (IBM): In IBM, a preform is first injected into a mould, then heated and blown to form its final shape. This process is favored for smaller, high-precision bottles and parts, especially those that require intricate designs.
- Injection Stretch Blow Moulding (ISBM): This advanced technique involves stretching the preform prior to blowing, enhancing the strength and clarity of the finished part. ISBM is often used for producing durable, high-quality bottles, commonly seen in the beverage industry.
Common Applications in Various Industries
The versatility of blow moulded plastic parts allows their widespread use across various industries. Here are some notable applications:
- Packaging Industry: Blow moulding is primarily used for manufacturing bottles and containers for beverages, personal care products, and household cleaners.
- Automotive Sector: Many automotive parts such as fuel tanks, air ducts, and various housing components are produced using blow moulding due to their lightweight and strong characteristics.
- Consumer Goods: Other products such as toys, buckets, and household storage solutions also rely on blow moulding to achieve their desired shapes and functionalities.
- Medical Field: The production of certain medical equipment, chambers, and bottles necessitates precision and reliability, which blow moulding effectively delivers.
Materials for Blow Moulded Plastic Parts
Popular Plastics Used in the Process
Choosing the right material for blow moulding is essential as it directly influences the properties of the final product. Common plastics used in blow moulding include:
- Polyethylene (PE): High-density polyethylene (HDPE) and low-density polyethylene (LDPE) are preferred for their durability, flexibility, and chemical resistance.
- Polypropylene (PP): Known for its toughness and resistance to harsh chemicals, PP is often used for various applications requiring flexibility and strength.
- Polyethylene Terephthalate (PET): This material is widely utilized for manufacturing bottles due to its excellent barrier properties and recyclability.
- Polyvinyl Chloride (PVC): Often used in applications where cost-effectiveness is a priority, PVC is versatile and offers good mechanical strength.
Advantages and Limitations of Different Materials
The selection of materials for blow moulded parts entails understanding the advantages and limitations of each type:
- Polyethylene: Advantages include excellent impact resistance and chemical stability. Limitations arise from lower temperature tolerance and UV degradation.
- Polypropylene: Benefits include high fatigue resistance and lightweight. However, it can be less effective in certain chemical environments.
- PET: Praised for its strength and clarity, its recyclability is a significant advantage, but it comes at a higher cost compared to alternatives.
- PVC: While it’s low-cost and versatile, concerns about its environmental impact and limited flexibility can be drawbacks.
Influence of Material Choice on Product Quality
The choice of material has a profound impact on the quality and functionality of blow moulded parts. Several factors to consider include:
- Durability: Materials must withstand stress and environmental factors relevant to their end-use.
- Weight: The material should provide strength without significantly increasing the product’s weight, which affects handling and shipping costs.
- Aesthetic Quality: Clarity and surface finish can be influenced by material choice, impacting consumer perception, particularly in packaging.
- Cost-effectiveness: While raw material pricing can vary, choosing materials that meet the performance criteria without excessive costs is crucial for profitability.
Design Considerations for Blow Moulded Parts
Key Factors in Designing Moulds
Successfully creating blow moulded parts requires careful consideration of mould design. Significant factors include:
- Mould Geometry: The design must accommodate the specific shape and features of the desired part while allowing the necessary stretching of the material.
- Draft Angles: Appropriate draft angles help facilitate the easy removal of parts from the mould without damaging them.
- Wall Thickness Uniformity: Ensuring consistent wall thickness promotes even cooling and strength in the final product.
- Material Flow: The design should support efficient material flow to avoid defects such as sagging or uneven surfaces.
Impact of Design on Manufacturing Efficiency
A well-structured design can greatly enhance the efficiency of the manufacturing process. Efficient designs can lead to:
- Reduced Cycle Times: Optimizing the design and moulding process helps decrease the time taken to produce each part, leading to increased output.
- Lower Energy Consumption: Efficient designs minimize energy requirements for heating the plastic and maintaining mould temperatures.
- Waste Reduction: Careful design mitigates excess material use and off-cuts, maintaining operational costs.
- Easier Maintenance: Simpler mould designs offer easier access for cleaning and maintenance, thus reducing downtime.
Examples of Effective Design Strategies
Numerous companies have effectively harnessed design strategies to improve blow moulding outcomes. Examples include:
- Integrating Features: Designing parts with integrated features, such as handles or spouts, can eliminate secondary operations and enhance functionality.
- Utilizing Simulation Software: Advanced 3D modelling and simulation software can predict how the material will behave during the moulding process, allowing for adjustments before production.
- Iterative Prototyping: Employing rapid prototyping techniques helps refine designs quickly and effectively identify flaws before mass production.
Quality Control in Blow Moulding
Techniques for Ensuring Quality in Production
Quality control is vital in the blow moulding process to ensure that parts meet required standards and specifications. Techniques include:
- Process Monitoring: Utilizing sensors and monitoring systems to track temperature, pressure, and material flow during production ensures consistent quality outcomes.
- Statistical Process Control (SPC): Applying SPC techniques allows manufacturers to identify variations in the production process and implement corrective actions as needed.
- Routine Inspections: Conducting regular inspections of finished goods can help detect defects, inform design changes, and maintain high quality in manufacturing.
Common Defects in Blow Moulded Plastic Parts
Defects can occur at various stages of the blow moulding process. Common issues include:
- Bubbles: Air entrapment within the material can lead to bubbles or voids in the finished part.
- Uneven Wall Thickness: This can result from improper material flow in the mould, affecting both aesthetics and strength.
- Warping or Shrinkage: Improper cooling and heating cycles can cause parts to warp or shrink beyond acceptable limits.
- Surface Defects: Scratches or irregularities can occur due to improper handling or foreign material contaminating the mould.
Best Practices for Quality Assurance
Implementing best practices can enhance overall quality assurance in blow moulding:
- Documenting Procedures: Creating comprehensive documentation regarding moulding processes, parameters, and guidelines promotes consistency and accountability.
- Employee Training: Regular training for employees on quality standards and defect identification ensures everyone is aligned with quality objectives.
- Utilizing Automation: Automation in process control can improve precision and reduce human error, enhancing overall product quality.
The Future of Blow Moulded Plastic Parts
Innovations in Blow Moulding Technology
The blow moulding industry is rapidly evolving with new technologies that enhance efficiency and quality. Key innovations include:
- 3D Printing Blows: Advances in 3D printing have led to faster prototyping of blow moulds, expediting product development timelines.
- Smart Technology Integration: Using IoT devices to monitor production processes allows manufacturers to implement predictive maintenance and optimize operations.
- Enhanced Materials: Ongoing research into bio-based and recycled plastics can lead to sustainable practices while maintaining product quality.
Trends Shaping the Industry
Several notable trends are influencing the future of blow moulding:
- Sustainability: There is an increasing demand for sustainable practices in manufacturing, including the use of recycled materials and eco-friendly production processes.
- Customization: As markets become more consumer-centric, manufacturers are adopting techniques that allow for greater customisation of products, enhancing user satisfaction.
- Global Supply Chain Optimization: Adjusting supply chains to cope with market fluctuations while ensuring quality and timely delivery is becoming increasingly important.
Sustainability Practices in Blow Moulding
Sustainability in the blow moulding industry is becoming essential, with companies adopting various practices:
- Material Recycling: Many manufacturers now focus on utilizing recycled plastics, reducing waste, and promoting circular economy models.
- Energy Efficiency: Implementing energy-efficient machines and processes can substantially decrease energy consumption and emissions during production.
- Waste Management: Strategies for reducing scrap and optimizing material usage are becoming increasingly common, as businesses recognize the financial and environmental benefits.