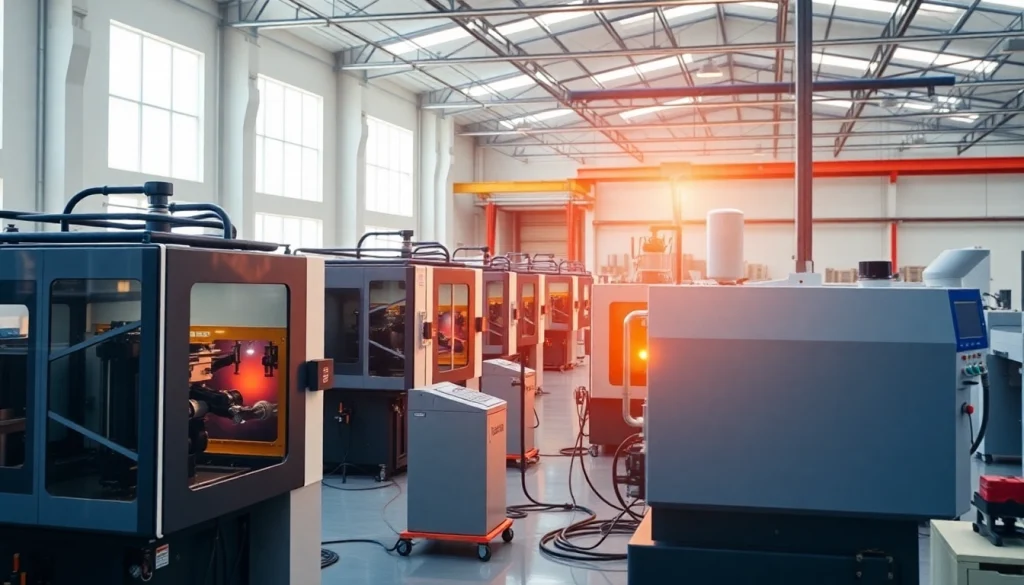
Understanding Injection Molding
What is Injection Molding?
Injection molding is a manufacturing process for producing parts by injecting molten material into a mold. It is most commonly used for fabricating plastic parts, which can be found in countless everyday products, including automotive parts, toys, and appliances. A wide variety of materials can be used in injection molding, with thermoplastics being the most prevalent due to their ability to be remelted and reused, making the process both versatile and sustainable.
How Injection Molding Works
The injection molding process begins with the creation of a mold, which is a hollow metal block designed to create the shape of the desired part. The following steps outline the typical injection molding process:
- Material Preparation: The process starts with the selection of raw materials, typically in the form of plastic pellets. These pellets are fed into a heating chamber where they are melted down into a viscous liquid.
- Injection: The molten plastic is then injected into the mold at high pressure using a specialized injection machine. This pressure ensures that the material fills all corners of the mold.
- Cooling: Once the mold is filled, the material is allowed to cool and harden. The cooling time can vary based on the size and thickness of the part.
- Mold Opening: After the plastic has cooled and solidified, the mold is opened, and the newly formed part is ejected.
- Finishing: The part may undergo additional processes such as trimming, painting, or assembly to complete the production.
Injection molding can produce a high volume of parts quickly and with exceptional precision, making it an ideal choice for manufacturers seeking efficiency and quality.
Industry Applications of Injection Molding
Injection molding is utilized across various industries due to its efficiency and capability for producing high-quality components. Some prominent sectors benefiting from this technology include:
- Automotive: Parts such as dashboards, lenses, and clips are molded from durable plastics.
- Consumer Electronics: Covers and housings for devices like phones and tablets are often created using injection molding due to tight tolerances and intricate designs.
- Medical: Surgical instruments and parts of diagnostic devices require sterile and precise components, achievable through injection molding.
- Packaging: Containers, caps, and closures for various products are typically produced using this method.
- Toys: Durable, colorful toys are commonly molded using injected plastics, making them both safe and appealing to consumers.
Choosing the Right Injection Molding Company
Factors to Consider When Evaluating Companies
Choosing the right injection molding company is critical to the success of your project. Here are several factors to consider:
- Experience and Expertise: Investigate the company’s experience in your specific industry and the types of materials they work with. Companies with extensive experience are more likely to understand the nuances of your requirements.
- Technology and Equipment: Modern and well-maintained machinery can significantly affect the quality and speed of production. Ensure that the company has up-to-date technology that aligns with your project needs.
- Quality Control Procedures: Inquire about the quality assurance processes they have in place. Companies with rigorous quality control are less likely to produce defects.
- Production Capabilities: Understand their production capacity, especially if high-volume production is necessary for your project.
- Cost Structure: Get a clear understanding of their pricing model. Transparency in costs will help you budget effectively and avoid hidden fees.
Questions to Ask Potential Partners
When evaluating potential injection molding partners, ask the following questions:
- What is your lead time for production?
- Can you provide references or case studies from past clients?
- What are your capabilities regarding material selection?
- How do you handle issues related to quality control?
- Are you able to accommodate changes during the production process?
- What support do you offer after the parts are produced (e.g., distribution, assembly)?
Reading Customer Reviews and Case Studies
Understanding the experiences of previous clients can give you insight into a company’s reliability and service level. Look for case studies on their website, and check third-party review sites for customer feedback. Pay attention to:
- Success stories that align with your project requirements.
- Comments on timeliness and quality of service.
- Reviews regarding customer support and communication throughout the project.
Benefits of Using Injection Molding Services
Cost Efficiency and Scalability
One primary benefit of injection molding is its cost efficiency, especially for high-volume productions. The initial costs of creating molds can be significant; however, once molds are produced, the cost per unit decreases dramatically as production scales up. This makes injection molding an attractive choice for products requiring large quantities.
Precision and Quality Assurance
Injection molding is renowned for its accuracy. The process allows for tight tolerances, ensuring that parts are produced to the exact specifications consistently. This level of precision minimizes waste and the need for post-production adjustments, ultimately saving time and money.
Environmentally Friendly Practices
Modern injection molding companies are increasingly adopting environmentally friendly practices. Closed-loop systems, material recycling, and the use of biodegradable materials are becoming standard in the industry. By choosing an eco-conscious partner, businesses can align with sustainability goals, reducing their overall environmental footprint.
Industry Best Practices in Injection Molding
Maintaining Equipment and Technology
Regular maintenance of injection molding machines is vital to ensure consistent performance and minimize downtime. Companies should invest in routine servicing and keep technologies up to date. This can involve employing skilled technicians who regularly inspect machines, calibrate settings, and replace any outdated components.
Quality Control Processes
Implementing robust quality control processes is essential for any injection molding company. This can include:
- In-Process Inspections: Conduct regular checks during production to catch defects early.
- Final Product Testing: Prior to shipping, every product should undergo testing for functionality and appearance.
- Feedback Loops: Establish systems for gathering and analyzing customer feedback to enhance future production runs.
Continuous Improvement and Innovation
To remain competitive, injection molding companies must embrace a culture of continuous improvement. This can involve employee training, experimenting with new materials, and adopting new technologies that enhance efficiency. Techniques like Lean Manufacturing can help streamline processes and reduce waste.
Future Trends in the Injection Molding Industry
Emerging Technologies and Materials
The injection molding industry is witnessing rapid advancements in technology, including the use of 3D printing for rapid prototyping and mold-making. Additionally, the development of advanced materials such as biodegradable plastics and high-performance composites is expanding the possibilities of what can be achieved through injection molding.
Sustainability Trends in Production
As sustainability becomes increasingly important to consumers, injection molding companies are adapting their practices. This includes utilizing recycled materials in production and improving energy efficiency in manufacturing processes. Companies embracing these changes can not only reduce their environmental impact but also appeal to eco-conscious consumers.
The Rise of Smart Manufacturing
Smart manufacturing, characterized by automation and data exchange, is transforming the injection molding industry. Companies using IoT devices can monitor machine performance in real time, resulting in proactive maintenance and increased efficiencies. These innovations are paving the way for greater productivity and lower costs in injection molding operations.